Positive Material Identification
Ensuring Material Quality and Traceability
Positive Material Identification (PMI) inspection is a critical component of quality control and safety assurance across various industries. This non-destructive testing (NDT) method is employed to verify the chemical composition of materials, ensuring that they meet specified requirements and standards. PMI is instrumental in preventing material mix-ups, enhancing product traceability, and mitigating the risk of catastrophic failures. In this comprehensive 600-word exploration, we delve into the intricacies of PMI inspection, its significance, methodologies, and its crucial role in modern quality assurance and materials management.
The essence of P.M.I. Inspection
Positive Material Identification (PMI) inspection is a non-destructive testing technique used to determine the chemical composition of materials, especially metals and alloys. It ensures that the material’s composition aligns with specified requirements, such as those outlined in industry standards or customer specifications. PMI is essential for verifying that materials used in critical applications, such as aerospace, nuclear, and petrochemical industries, are of the correct grade and do not pose risks associated with incompatible materials.
Applications across Industries.
Want a chat?
Take me back
The P.M.I. Inspection Procedure
Preparation: The inspection area is prepared by cleaning the surface of the material to remove contaminants or oxidation that could interfere with accurate testing.
Instrument Selection: Specialised PMI instruments, such as handheld X-ray fluorescence (XRF) analysers or optical emission spectrometers (OES), are selected based on the material type, application, and required accuracy.
Sample Collection: A small sample, often in the form of a disc or a chip, is collected from the material to be analysed.

Analysis: The sample is subjected to analysis using the selected PMI instrument. XRF analysers use X-ray emissions to determine elemental composition, while OES instruments utilize optical emissions to identify elements.
Data Interpretation: The data obtained from the analysis is interpreted to determine the chemical composition of the material. It is compared against specified requirements to verify conformance.
Reporting: Inspection findings, along with the composition analysis results, are documented in a comprehensive report. This report serves as a record for quality control, material certification, and regulatory compliance.
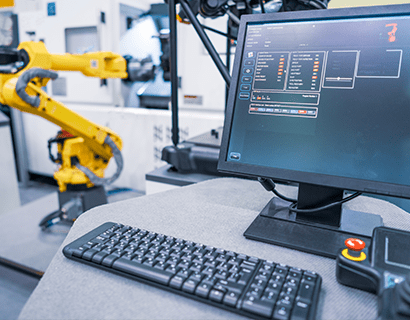
Advantages of P.M.I. Inspection
Material Traceability: It enhances material traceability by providing documented evidence of material composition throughout the supply chain.
Quality Assurance: PMI ensures that materials meet specified requirements, reducing the risk of defects and ensuring product quality.
Safety: PMI prevents material mix-ups that could lead to catastrophic failures, especially in safety-critical applications.
Regulatory Compliance: PMI helps industries meet regulatory and safety standards by verifying material composition.
Efficiency: PMI reduces the need for expensive and time-consuming destructive testing methods, such as chemical analysis.
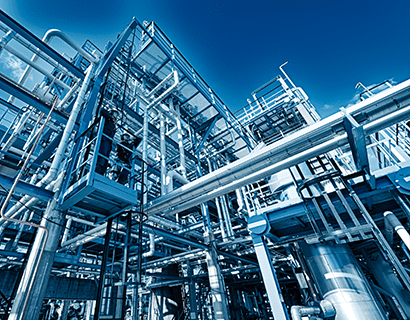