M.P.I.
Magnetic Particle Inspection
#thinkNDTi offers a comprehensive Magnetic Particle Inspection Service using our vast network of experienced technicians covering the whole of the U.K.
Detecting surface defects in ferrous materials
Magnetic Particle Inspection is a highly effective non-destructive testing method specifically designed to detect surface and near-surface defects in ferrous materials. This technique is celebrated for its precision in revealing cracks, fractures, and other irregularities that may compromise the structural integrity of a component. At its core, M.P.I. capitalises on the magnetic properties of ferromagnetic materials, which become magnetised when subjected to a magnetic field.
Applications across Industries.
Want a chat?
Take me back
The MPI Procedure
The MPI procedure is a systematic process that unfolds in several key steps:
Magnetisation: The component under inspection is subjected to a magnetic field, either through direct contact using a yoke or by employing a magnetic coil. This magnetisation induces a magnetic flux in the material, which enhances its susceptibility to magnetic particle attraction.
Application of Magnetic Particles: A suspension of fine magnetic particles, often in a liquid carrier, is applied to the surface of the magnetised component. These particles, typically iron filings or iron oxide, adhere to the surface and collect at areas of magnetic flux leakage, which corresponds to defects or cracks.
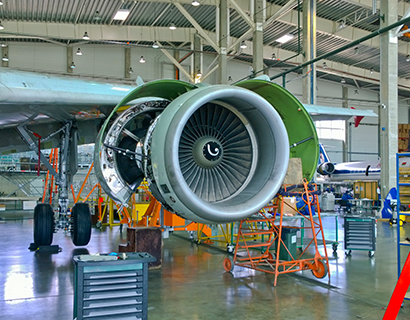
Inspection: A trained inspector closely examines the component’s surface under suitable lighting conditions. Any accumulation of magnetic particles forms a visible indication, delineating the extent and nature of the defects.
Evaluation and Reporting: The inspector evaluates the indications, considering their size, shape, and location. These observations are meticulously documented in a report, serving as a comprehensive record of the inspection findings.
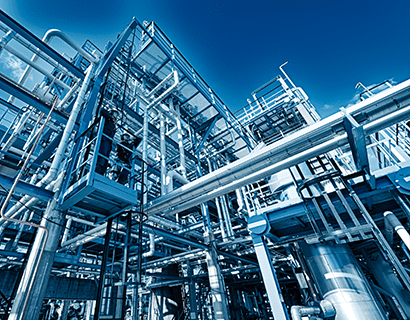
Advantages of MPI
Magnetic Particle Inspection can detect surface and near-surface defects in ferrous materials, providing precise and reliable results.
Speed: The inspection process is relatively rapid, making it an excellent choice for high-throughput operations.
Versatility: MPI is particularly well-suited for ferrous materials but can also be adapted for inspecting non-ferrous materials with the use of specialized techniques.
Cost-Efficiency: Compared to other NDT methods, MPI is cost-effective, making it accessible for routine inspections and quality control processes.
Non-Destructive: MPI does not harm the integrity of the inspected component, allowing it to be used without damage.
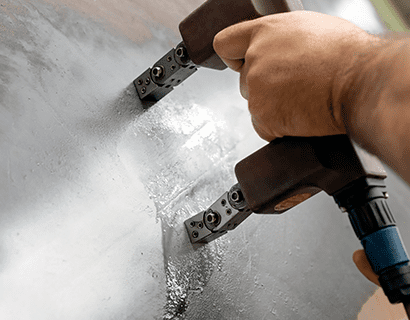